µ§¼Ò´Â 1949³â¿¡ ¼³¸³ÇØ Â÷·® ¿¡¾îÄÁ, ÀüÀÚ Á¦¾î ½Ã½ºÅÛÀ» ºñ·ÔÇÑ ¼±Áø ÀÚµ¿Â÷ ±â¼ú, ½Ã½ºÅÛ, Á¦Ç°À» ¼¼°è ÁÖ¿ä ÀÚµ¿Â÷ Á¦Á¶ ȸ»ç¿¡ °ø±ÞÇÏ´Â ÀÚµ¿Â÷ ºÎǰ Á¦Á¶ ȸ»ç´Ù. µ§¼Ò´Â ȯ°æ ÁöħÀ¸·Î 2000³â 6¿ù <µ§¼Ò ºñÀü 2005>¿Í 2005³â 11¿ù <µ§¼Ò ºñÀü 2015>¸¦ °øÇ¥Çϰí 'ȯ°æ Á¶È¸¦ ¸ñÇ¥·Î ÇÑ ¿¬±¸ ¡¤ °³¹ß°ú ÀÚ¿¬ ȯ°æ º¸ÀüÀ» ÅëÇØ »ç¶÷µéÀÇ Çູ¿¡ °øÇåÇÒ °Í'À» ¼±¾ðÇß´Ù.
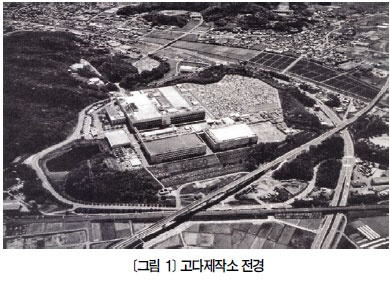 µ§¼Ò °í´Ù(ú¹ï£)Á¦ÀÛ¼Ò´Â ÀϺ» ³» 7¹øÂ° Á¦ÀÛ¼Ò·Î, 1987³â 4¿ù Á¶¾÷À» ½ÃÀÛÇß´Ù. óÀ½ºÎÅÍ '¾ÈÀüÇϰí ģȯ°æÀûÀΠŬ¸° °øÀå'À» ÄܼÁÆ®·Î ³»¼¼¿ö ¾ÈÀü ¡¤ ȯ°æÀ» Áß½ÃÇÑ »ý»ê Ȱµ¿À» ÃßÁøÇØ ¿Ô´Ù. 1997³â 10¿ù¿¡ ISO 14001, 2001³â 2¿ù¿¡ ÀϺ» °æÁ¦»ê¾÷±¹Àå»ó(¿¡³ÊÁö °ü¸® ¿ì·® °øÀå), 2004³â 3¿ù¿¡ ISO/TS 16949 ÀÎÁõÀ» ÃëµæÇß´Ù. ¶ÇÇÑ, 2002³â 8¿ù¿¡ Á¦·Î À̹̼ÇZero Emission(°øÀå Æó±â¹° Á¦·Î)À» ´Þ¼ºÇÏ´Â ÇÑÆí, ¿¡³ÊÁö Àý¾à Ȱµ¿¿¡µµ Àû±Ø ÀÓÇϰí ÀÖ´Ù. ±×µ¿¾È ÃÑ·ÂÀ» ±â¿ï¿© ¿Â ¿¡³ÊÁö Àý¾à Ȱµ¿ÀÇ ¼º°ú°¡ ³ôÀº Æò°¡¸¦ ¾ò¾î 2008³â 2¿ù '2007³âµµ ¿¡³ÊÁö °ü¸® ¿ì·® °øÀå'ÀϺ» ÀÚ¿ø¿¡³ÊÁöû Àå°ü ǥâÀ» ¹Þ¾ÒÀ¸¸ç, ±× Ȱµ¿ÀÇ ÀÏ·Ê·Î ¼¼°èÀû ¼öÁØÀÇ Å¬¸°·ëÀ» º¸À¯ÇÑ °í´ÙÁ¦ÀÛ¼Ò ³» ¿ì¿¡ÇÏ °øÀå¿¡¼ °³¼± È¿°ú¸¦ °ÅµÐ »ç·Ê¸¦ ¿©±â¿¡ ¼Ò°³ÇÑ´Ù.
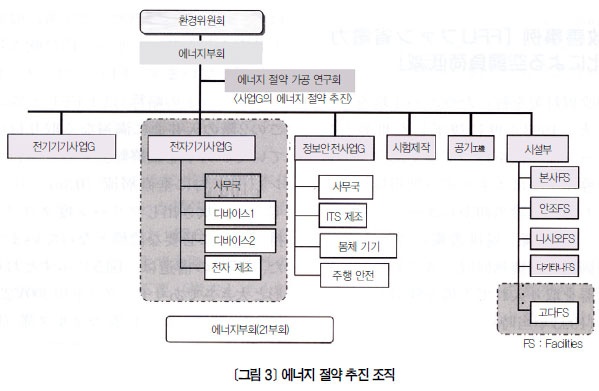 * À§ À̹ÌÁö¸¦ Ŭ¸¯ÇϽøé Å©°Ô º¸½Ç ¼ö ÀÖ½À´Ï´Ù.
¿¡³ÊÁö »ç¿ë »óȲ °í´ÙÁ¦ÀÛ¼ÒÀÇ ¿¡³ÊÁö »ç¿ë »óȲÀº <±×¸² 2>¿Í °°À¸¸ç, °¢ ¿¡³ÊÁö¸¦ CO©ü(t-CO©ü) ºñÀ²·Î ³ªÅ¸³Â´Ù. ³»¿ªÀ» »ìÆìº¸¸é Àü±â°¡ ÀüüÀÇ 60%¸¦ Â÷ÁöÇÑ´Ù. Àü±â¿¡¼ ¹èÃâµÈ CO©ü¾çÀ» °øÀ庰·Î º¸¸é ¿ì¿¡ÇϰøÀåÀÌ ¾à 40%·Î ´ëºÎºÐÀ» ¹èÃâÇÑ´Ù. ¼Ò°³ÇÒ °³¼±»ç·Ê´Â °í´ÙÁ¦ÀÛ¼Ò ³»¿¡¼ ¿¡³ÊÁö »ç¿ë·®ÀÌ ¸¹Àº ¹ÝµµÃ¼¸¦ Á¦Á¶ÇÏ´Â ¿ì¿¡ÇÏ °øÀåÀÇ È°µ¿ °á°ú º¸°í´Ù.
¿¡³ÊÁö Àý¾à ÃßÁø Á¶Á÷ ÃßÁø Á¶Á÷ | °øÀå¿¡¼ ³ª¿À´Â CO©ü¹èÃâ·® °¨Ãà ¸ñÇ¥¸¦ ´Þ¼ºÇϰíÀÚ <±×¸² 3>°ú °°ÀÌ È¯°æÀ§¿øÈ¸ ¾Æ·¡ ¿¡³ÊÁöºÎȸ¸¦ ¼³Ä¡Çß´Ù. ±¸¼º Á¶Á÷ Áß ÇϳªÀÎ °í´ÙÁ¦ÀÛ¼ÒÀÇ ¿¡³ÊÁö Àý¾à Á¶Á÷Àº <±×¸² 3>¿¡¼ Á¡¼±À¸·Î µÑ·¯½ÎÀÎ ºÎºÐÀÌ´Ù. °í´ÙÁ¦ÀÛ¼Ò Á¶Á÷ÀÇ Æ¯Â¡Àº ¸ðµç ºÎ¼ÀÇ Âü°¡´Â ¹°·Ð, ȾÀû ¿¬°áÀ» °ÈÇÑ È°µ¿ÀÌ´Ù. ¿©±â¼± µð¹ÙÀ̽º Á¦Á¶2ºÎÀÇ È°µ¿ »ç·Ê¸¦ ¼Ò°³ÇÑ´Ù.
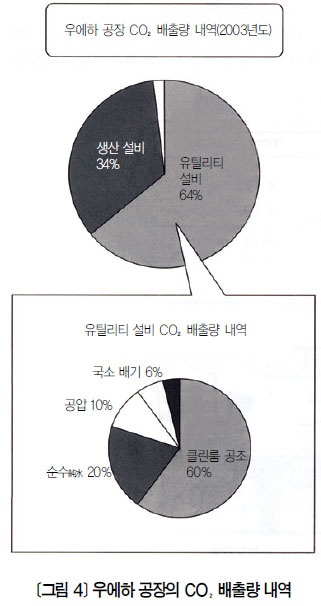 ¿¡³ÊÁö Àý¾à Ȱµ¿°ú ÁÖ¿ä ½Çõ Ç׸ñ | µð¹ÙÀ̽º Á¦Á¶2ºÎÀÇ ¿¡³ÊÁö Àý¾à Ȱµ¿Àº <±×¸² 4>¿¡¼ º¸µíÀÌ À¯Æ¿¸®Æ¼ ¼³ºñ°¡ Àü±â ¿¡³ÊÁöÀÇ 64%¸¦ Â÷ÁöÇÑ´Ù. ±× Áß¿¡¼µµ Ŭ¸°·ë °øÁ¶°¡ 60%·Î ÃÖ´Ù ¹èÃâ·®À̱⿡, ÀÌ ºÎºÐÀÇ CO©ü¹èÃâ·® °¨ÃàÀ» ÁÖµÈ ¸ñÇ¥·Î ¨ç °íÈ¿À²È, ¨è Àú¿ë·®È, ¨é ¼Õ½Ç ÃÖ¼ÒÈ, ¨ê ÀÚ¿¬ ¿¡³ÊÁö ÀÌ¿ëÀ» ¿°µÎ¿¡ µÎ°í ¾ÆÀ̵ð¾î¸¦ ¸ðÀ¸°í »ç³»¿Ü »ç·Ê¸¦ öÀúÈ÷ ºÐ¼®Çß´Ù. 2000³â ÀÌÈÄ ½Ç½ÃÇÑ ÁÖ¿ä Ç׸ñÀº <Ç¥ 2>¿Í °°´Ù.
°³¼± »ç·Ê-FFU ÆÒ Àü·Â Àý¾àÀ¸·Î °øÁ¶ ºÎÇÏ Àú°¨ À̹ø¿¡ °³¼± ´ëÃ¥À» ½Ç½ÃÇÑ ¿ì¿¡ÇÏ °øÀåÀº 1993³â¿¡ ÁذøÇÑ ¼¼°è À¯¼öÀÇ Å¬¸°·ëÀ» º¸À¯ÇÑ °øÀåÀÌ´Ù. ÈçÈ÷ ¹ÝµµÃ¼ °øÀåÀº ¿¡³ÊÁö »ç¿ë·®ÀÌ Å©°í ¸¹±â¿¡ °Ç¼³ ÃʺÎÅÍ À¯Æ¿¸®Æ¼ ¼³ºñ·Î °øÁ¶, ±¹¼Ò ¹è±â¼³ºñÀÇ ÆÒ µî INV Á¦¾î ¡¤ ¿ÜÁ¶±â ¿ ȸ¼ö ½Ã½ºÅÛ µî ¿¡³ÊÁö Àý¾à ±â±â¸¦ µµÀÔÇØ °øÀåÀ» °Ç¼³Çß´Ù(1993³â ´ç½Ã).
¿ì¿¡ÇÏ °øÀåÀÇ Å¬¸°·ëÀº <±×¸² 5>¿Í °°ÀÌ 3°ã ±¸Á¶·Î µÅ ÀÖ´Ù. 2Ãþ ºÎºÐÀÌ ³ôÀº Á¤¹Ðµµ·Î Ãʹ̼¼ °¡°øÀ» ÇÏ´Â ¿ì¿¡ÇÏ »ý»ê Ç÷ξî¸ç, ÀÌ Ç÷ξîÀÇ Å¬¸°µµ, ¿Âµµ, ½Àµµ¸¦ ÀÏÁ¤ÇÏ°Ô À¯Áö °ü¸®ÇÑ´Ù. Ŭ¸°·ë °øÁ¶´Â ¹Ù±ù°ø±â¸¦ ¿Â ¡¤ ½Àµµ Á¶Á¤ÇØ 1ÃþÀ¸·Î º¸³½ ÈÄ ÃµÀåÀ» ÅëÇØ Ŭ¸°·ë ³»ºÎ·Î µé¾î°¡´Â ÇüÅ·Π¼øÈ¯ÇÑ´Ù. FFU¶õ ÆÒ ÇÊÅÍ À¯´ÖÀÇ ¾àĪÀ¸·Î, 2Ãþ õÀå¿¡ °í¸£°Ô ¼³Ä¡ÇØ ¸ÕÁö¸¦ ÃÖÁ¾ Á¦°ÅÇÏ´Â µ¿½Ã¿¡ Ŭ¸°·ë ³»¿¡ ¼öÁ÷ Ãþ·ù(0.3m/ÃÊ)·Î °ø±â¸¦ ³»»Õ¾î Ŭ¸°µµ µî±Þ 1À» À¯ÁöÇÏ´Â µ¥ ÇÊ¿äÇÑ ¼³ºñ´Ù. FFUÀÇ ±¸Á¶´Â <±×¸² 5>¿Í °°Àº ¿ÜÇü°ú Å©±â¸ç ¸ðÅÍ(´Ü»ó 200V 230W), ÆÒ, ¹æÀ½ À¯´ÖºÎ, ÇÊÅͺÎ(ULPA ÇÊÅÍ 0.1§ 99.9999% Á¦°Å)·Î ±¸¼ºµÈ´Ù. ¿ì¿¡ÇϰøÀå¿¡ 2464´ë¸¦ ¼³Ä¡ÇßÀ¸¸ç, 24½Ã°£ 365ÀÏ ¿¬¼Ó ¿îÀüÇÑ´Ù.
°³¼± ³»¿ë | FFU´Â Ŭ¸°·ë õÀå¿¡ ¼³Ä¡ÇÑ °ÍÀ¸·Î °øÁ¶ÀÇ °ø±â ¼øÈ¯ ºÎºÐ¿¡ ¼ÓÇϱ⿡ ÆÒÀÇ ¿îÀü µ¿·ÂÀ¸·Î Àü±â¸¦ ¼ÒºñÇÒ »Ó ¾Æ´Ï¶ó ¸ðÅÍ ¹ß¿¿¡ µû¸¥ °øÁ¶ ºÎÇϰ¡ ÇÔ²² Áõ°¡ÇÑ´Ù. µû¶ó¼ ÇöÀç »ç¿ëÇÏ´Â °Íº¸´Ù ¼Òºñ Àü·ÂÀÌ ³·Àº FFU·Î ±³Ã¼ÇÑ´Ù¸é Àü±â ¼Òºñ·®°ú °øÁ¶ ºÎÇϸ¦ µ¿½Ã¿¡ ³·Ãâ ¼ö ÀÖ´Ù´Â µ¥ Âø¾ÈÇÏ°í °³¼±¾ÈÀ» °ËÅäÇß´Ù. ¿ì¼± FFU ¼±Á¤¿¡ ÀÖ¾î FFU º»Ã¼¿¡¼ ¼Õ½ÇÀÌ ¹ß»ýÇÏÁö ¾Ê´ÂÁö ±¸Á¶ ÀÚü¸¦ »ìÆñ´Ù. ÁÖ¸ñÇÑ °ÍÀº <±×¸² 6>¿¡¼ º¸ÀÌ´Â ¹æÀ½ À¯´ÖºÎÀÇ ¾Ð·Â ¼Õ½Ç·Î, Çʿ伺 ¿©ºÎ¸¦ °ËÅäÇÑ °á°ú ºÒÇÊ¿ä(¾ø¾Öµµ »ç³» ¼ÒÀ½Ä¡ ±âÁØÀ» ¸¸Á·)ÇÏ´Ù°í ÆÇ´ÜÇØ ¹æÀ½ À¯´ÖÀÌ ¾ø´Â ±¸Á¶¿¡´Ù Ŭ¸°·ëÀÇ È¯°æ À¯Áö¿¡ ÇÊ¿äÇÑ Ç³·® 13.5§©/min È®º¸¸¦ Á¶°ÇÀ¸·Î °¢ Á¦Á¶»ç¸¦ ºñ±³ °ËÅäÇß´Ù. ÅõÀÚ ´ë È¿°úµµ Áß¿äÇÑ °ËÅä Ç׸ñÀ̱⿡ ÅõÀÚÀý°¨¾Èµµ ÇÔ²² °ËÅäÇß´Ù. ±× °á°ú, <±×¸² 7>¿¡¼ º¸µíÀÌ ÅõÀÚ ´ë È¿°ú°¡ °¡Àå ¿ì¼öÇϰí CO©ü¹èÃâ·®µµ ÃÖ¼ÒÀÎ A»ç Á¦Ç°(dz·® 13.5§©/min×±â¿ÜÁ¤¾Ð50Pa×70W)À» ¼±ÅÃÇß´Ù. °³¼±Á¡À¸·Î ¿ì¼± FFUº»Ã¼ÀÇ ¾Ð·Â ¼Õ½ÇÀ» ³·Ãß°íÀÚ ÇöÀçÀÇ FFU ¹æÀ½ À¯´ÖºÎ¸¦ ¾ø¾Ý´Ù. ½Ã·ÎÄÚÆÒSirocco FanÀ» °íÈ¿À² Åͺ¸ÆÒÀ¸·Î º¯°æÇϰí, ¸ðÅ͵µ ´Ü»ó 200V¸¦ °íÈ¿À² »ï»ó 200V ¸ðÅÍ·Î ¹Ù²ã ¼Òºñ Àü·ÂÀ» 230W¿¡¼ 70W·Î ÁÙ¿´´Ù. ¶ÇÇÑ, ÅõÀÚ ºñ¿ëÀ» ÁÙÀ̰íÀÚ ¼±Á¤¿¡ ¾Õ¼ ULPA ÇÊÅÍ ºÎºÐÀº dz¼ÓÀ» ÃøÁ¤ÇÏ°í ´É·ÂÀ» ÆÇÁ¤Çß´õ´Ï ÃæºÐÈ÷ »ç¿ë °¡´ÉÇÑ °ÍÀ¸·Î ÆÇ´ÜÇØ °»½ÅÇÏÁö ¾Ê°í ±âÁ¸ °ÍÀ» ¾²±â·Î Çß´Ù.
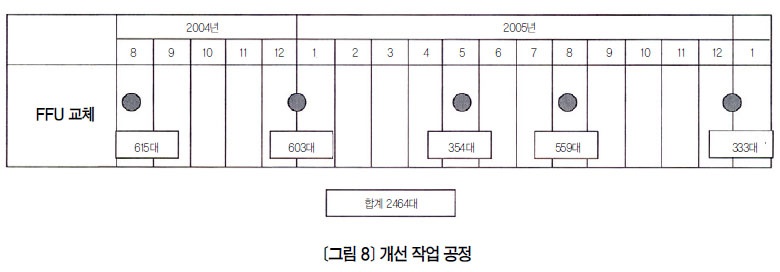 * À§ À̹ÌÁö¸¦ Ŭ¸¯ÇϽøé Å©°Ô º¸½Ç ¼ö ÀÖ½À´Ï´Ù.
°³¼± È¿°ú | °³¼± ½Ç½Ã »óȲÀÇ °øÁ¤Àº <±×¸² 8>°ú °°´Ù. ÀÛ¾÷Àº °¡µ¿ ÁßÀÎ °øÀå¿¡ ¿µÇâÀ» ÁÖÁö ¾Êµµ·Ï ÁÖÀǸ¦ ±â¿ï¿© »ý»ê°ú°¡ °¡µ¿ÇÏÁö ¾Ê´Â Àå±â ¿¬ÈÞ(º½, ¿©¸§, °Ü¿ï) Áß¿¡ Á¦Ç°, »ý»ê ¼³ºñ¿¡ ¸ÕÁö µîÀÌ ºÙÁö ¾Êµµ·Ï Á¶Ä¡¸¦ ÃëÇϰí 1ȸ´ç ¼ö¹é ´ë¾¿À» ±³Ã¼ÇØ 2004~2005³â 2³â°£ ÃÑ 5ȸ¿¡ °ÉÃÄ ÀÛ¾÷ÇßÀ¸¸ç, FFU ÃÑ 2464´ëÀÇ Àü·ÂÀ» Àý¾àÇß´Ù. Á¤¸®Çϸé FFU ÃÑ 2464´ëÀÇ Àü·Â Àý¾àÀ¸·Î FFUÀü·Â 3450§Óh/³â ¡¤ 1316t-CO©ü/³âÀ¸·Î Å©°Ô ³·ÃèÀ¸¸ç, ¹ß¿·® Àú°¨À¸·Î °øÁ¶ ºÎÇÏ 966§Óh/³â ¡¤ 368t-CO©ü/³âÀ» Àú°¨Çß´Ù. ±× °á°ú, CO©ü¸¦ ÇÕ°è 1684t-CO©ü/³âÀ» ÁÙÀÎ µ¿½Ã¿¡ ¿¡³ÊÁö ºñ¿ë 7,300¸¸ ¿£/³âÀ» Àý°¨Çß´Ù.
*
ÀÌ FFUÀÇ ¿¡³ÊÁö Àý¾à ´ëÃ¥Àº »ç³» µ¿ÀÏÇÑ ½Ã¼³À» °¡Áø ¾ÆÀÌÄ¡Çö ´Ö½Å½Ã¿¡ ÀÖ´Â µ§¼Ò ±âÃÊ¿¬±¸¼Ò¿¡µµ 2006³âºÎÅÍ 2007³â¿¡ °ÉÃÄ °ø»ç¸¦ ½Ç½ÃÇØ CO©ü°¨Ãà È¿°ú¸¦ ¿Ã·È´Ù. ¶ÇÇÑ, 2006³â 3¿ù¿¡ ÁöÁø ½Ã Áøµ¿À» ÁÙÀÌ´Â ±¸Á¶¸¦ äÅÃÇÑ ¿ì¿¡ÇÏ ½Å°øÀåÀÌ °í´ÙÁ¦ÀÛ¼Ò ³»¿¡ ÁذøÇߴµ¥, ±×µ¿¾È ½Ç½ÃÇØ ¿Â ¿¡³ÊÁö Àý¾à Á¶°Ç°ú ½Å±â¼úÀ» °Ç¼³ ´Ü°èºÎÅÍ µµÀÔÇß´Ù. FFUÀÇ °æ¿ì »ý»ê ÀåÄ¡, Á¦Ç°ÀÇ ¹Ý¼Û ¹æ¹ý °³¼±À¸·Î Ŭ¸°µµ Á¶°ÇÀ» ¿ÏÈ(µî±Þ 1À» µî±Þ 1¸¸À¸·Î ¿ÏÈ)ÇÏ´Â µ¿½Ã¿¡ FFU¸¦ ´ëdz·®ÈÇØ FFU ´ë¼ö¸¦ Å©°Ô ÁÙ¿´´Ù. ¿ì¿¡ÇÏ ½Å°øÀåÀº §³´ç CO©ü¹èÃâ·®À» ±âÁ¸ ¿ì¿¡ÇÏ °øÀå ´ëºñ 20% °¨ÃàÇß´Ù. °Ô´Ù°¡ ½Å°øÀåÀÇ ¿¡³ÊÁö Àý¾à ¾ÆÀÌÅÛÀ» ±âÁ¸ °øÀå¿¡ Çǵå¹éÇØ °³¼±ÇØ ³ª°¡°í ÀÖ´Ù. 'Áö±¸ ȯ°æ º¸È£°¡ ÀηùÀÇ °¡Àå ±ÞÇÑ °úÁ¦´Ù'¶ó´Â ÀνÄÀ» Åä´ë·Î µ§¼Ò ±×·ìÀº ±â¾÷ Çൿ ¼±¾ð Áß ÇϳªÀÎ '»çȸ¿Í °ø»ýÀ» ¸ñÇ¥·Î »ç¾÷ Ȱµ¿À» ÇÏ´Â ¸ðµç Áö¿ª¿¡¼ »çȸ °øÇå Ȱµ¿¿¡ ÆîÄ£´Ù'¿¡ ±Ù°ÅÇØ °í´ÙÁ¦ÀÛ¼ÒÀÇ ¿¡³ÊÁö Àý¾à Ȱµ¿À» ¼Ò°³Çß´Ù. À̹ø »ç·Ê´Â ¿ì¿¡ÇÏ °øÀåÀÇ Å¬¸°·ëÀ̶ó´Â Ư¼ö ȯ°æ¿¡¼ ÀÌ·ïÁø Ȱµ¿ÀÌÁö¸¸, Âü°íÇØ Áö±¸ ȯ°æ º¸È£¿¡ ÀÛÁö¸¸ µµ¿òÀÌ µÇ¸é ÁÁ°Ú´Ù.
Á¤¸® ÀüÈ¿µ ±âÀÚ
<±¹³» »ç·Ê>
»ï¼ºÀüÀÚ
»ï¼ºÀüÀÚÀÇ »ç¾÷ ºÐ¾ß´Â Å©°Ô ¿ÏÁ¦Ç° ºÎ¹®°ú ºÎǰ ºÎ¹®À¸·Î ³ª´¶´Ù. ¿ÏÁ¦Ç° ºÎ¹®¿¡ TV, ³ÃÀå°í, ¿¡¾îÄÁ, ¼¼Å¹±â µî °¡ÀüÁ¦Ç°, ÈÞ´ëÀüÈ, °³Àοë ÄÄÇ»ÅÍ, MP3 Ç÷¹ÀÌ¾î µîÀÌ ¼ÓÇϸç, ºÎǰ ºÎ¹®Àº ¹ÝµµÃ¼(¸Þ¸ð¸® ¹ÝµµÃ¼, ½Ã½ºÅÛ LSI ¹ÝµµÃ¼)¿Í LED·Î ÀÌ·ïÁø´Ù. ±×Áß »ï¼ºÀüÀÚÀÇ TV »ê¾÷Àº ÈÞ´ëÀüÈ¿Í ÇÔ²² »ï¼ºÀÇ ¿ÏÁ¦Ç° »ç¾÷ ºÐ¾ßÀÇ ÇÙ½É µ¿·ÂÀÌ´Ù. LED TV´Â ÃÖ±Ù Æø¹ßÀûÀ¸·Î ¼ºÀåÇØ TV ºÐ¾ßÀÇ ¼ºÀåÀ» À̲ô´Â ÁßÃß ºÐ¾ß·Î ¶°¿Ã¶úÀ¸¸ç, LCD TV¿Í ¸ð´ÏÅÍ ¿ª½Ã °¢°¢ ÇØ´ç ºÐ¾ß¿¡¼ ¼±µÎ¸¦ Áö۰í ÀÖ´Ù. ¾ÕÀ¸·Îµµ ²÷ÀÓ¾ø´Â Çõ½Å, 3D ºÐ¾ß¿Í °°Àº ½Å±â¼ú ¹ßÀüÀ» ÅëÇØ ½ÃÀå Áö¹è·ÂÀ» ÁöÄѳª°¥ ¹æÄ§ÀÌ´Ù. ¿©±â¿¡ ¼Ò°³ÇÒ ³»¿ëÀº LCD »ç¾÷ºÎÀÇ ¿¡³ÊÁö Àý¾à »ç·Ê´Ù.
¼ö°¡½À ½Ã½ºÅÛ Àû¿ë ±×µ¿¾ÈÀº Áõ±â½Ç °¡½À ÀåÄ¡¸¦ ÀÌ¿ëÇØ ½Àµµ¸¦ Á¶ÀýÇßÀ¸¸ç, Áõ±â¸¦ °ø±ÞÇϱâ À§ÇØ LNG¸¦ ¿¬·á·Î º¸ÀÏ·¯¸¦ °¡µ¿Çß´Ù. ¶ÇÇÑ, ¿Âµµ Á¶ÀýÀ» À§ÇØ ³Ãµ¿±â¸¦ °¡µ¿ÇØ ³Ã±â¸¦ °ø±ÞÇß´Ù. ÀÌÈÄ Áõ±â½Ä °¡½À ÀåÄ¡¸¦ ´ë½ÅÇØ ¿¡¾î ½ºÇÁ·¹ÀÌ½Ä ¼öºÐ¹« °¡½À ÀåÄ¡¸¦ ¼³Ä¡ÇØ °¡½À¿ë Áõ±â »ý»êÀ» À§ÇÑ LNG»ç¿ë·®À» ¾ø¾Ö´Â ÇÑÆí, ¼ö°¡½À¿¡ ÀÇÇÑ Áõ¹ß Àá¿ Èí¼ö È¿°ú·Î ±âÁ¸ ¿Âµµ Á¶ÀýÀ» À§ÇØ °¡µ¿Çß´ø ³Ãµ¿±â¿ë Àü·Â »ç¿ë·®µµ Àý°¨Çß´Ù.
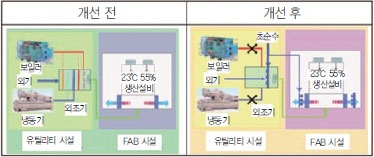 ¿ÜÁ¶±â Æó¿ ȸ¼ö¸¦ ÅëÇÑ LNG Àý°¨ »ï¼ºÀüÀÚ LCD »ç¾÷ºÎ´Â µ¿Àý±â ¿ÜÁ¶±â µ¿ÆÄ¸¦ ¹æÁöÇϰíÀÚ ¿¹¿ ¼³ºñ¿¡ Áõ±â¸¦ ¿¿øÀ¸·Î »ç¿ëÇØ ¿Ü±â À¯ÀÔ ¿Âµµ¸¦ ³ô¿© À¯ÀÔÇß´Ù. Áõ±â¸¦ °ø±ÞÇϱâ À§ÇØ LNG¸¦ ¿¬·á·Î º¸ÀÏ·¯¸¦ °¡µ¿ÇßÀ¸¸ç, ³Ã°¢Å¾¿¡¼ ¿ ±³È¯¿ë ³Ã°¢¼ö¸¦ ¼øÈ¯ÇØ »ç¿ëÇß´Ù. ÀÌ·¯ÇÑ Ã¼Á¦¸¦ °³¼±ÇØ ¿ÜÁ¶±â µ¿ÆÄ ¹æÁö¿ë ¿¿øÀ¸·Î Áõ±â ´ë½Å ³Ã°¢Å¾ ¼øÈ¯ ³Ã°¢¼ö(25¡É)¸¦ »ç¿ëÇÔÀ¸·Î½á Áõ±â »ý»êÀ» À§ÇÑ LNG »ç¿ë·®À» Àý°¨Çß´Ù.
¡Ø ÀÚ·á Ãâó : ¿¡³ÊÁö°ü¸®°ø´Ü <2009 ¿¡³ÊÁö Àý¾à ¿ì¼ö »ç·ÊÁý>> |
<Energy News>
http://www.energy.co.kr
|